Energy input and output
Fuel inputs to the sites have been reported in GJ. The lower calorific heat values have been used to calculate GJ from m3 or tonnes of fuel. Fossil fuel and biomass fuel have been reported separately. The energy figures for the sites include both energy for process and energy for infrastructure. No attempts have been made to differentiate between these two types of energy usage because process energy dominates (98% or more). Input of electricity into the sites is also reported. The electricity produced at the site itself is not reported. Some mills sell energy externally in the form of electricity, steam or warm water. The production sites are treated as a black box in the database, giving data on inputs and outputs only. Because no information is given about what happens within the box it is not possible to calculate an energy balance with the data in the database. Within this black box, energy is recovered through the burning of black liquor and bark from the wood coming in at production sites for primary fibre-based paper production. Most of the energy used in the process for Kraftliner production comes from internal burning of the black liquor. This inherent energy is not reported as part of the fuel input in the gate-to-gate inventory, although it is reported separately in Table 5. The total energy input for the process for Kraftliner production including the black liquor burning is around 14 GJ/tonne. The total energy input for the process of Semi Chemical Fluting production is around 10 GJ/tonne. The total energy input for the process of testliner and recycled fluting production is around 7 GJ/tonne. Combined heat power generation is applied at most of the production sites for recycled fibre based paper, but not always in the same way. The combined heat power generation can cover all or part of the steam consumption (Figure 12). When it covers only part of the steam consumption, then additional boilers also produce steam. The process always uses more heat (steam) than electricity. Therefore, when the installation is designed to cover the whole steam consumption more electricity is generated than is needed for the process. The excess of electricity is sold to the public grid. There are two possible ways of treating this excess electricity in an LCA.
a. The production of electricity is an integral part of the paper production: it would not be produced if the paper were not produced. Paper is thus considered as the only “product” of the process. In an LCA this would mean that electricity generation for the public grid is “saved” when an excess of electricity produced at a paper mill is sold to the public grid. Thus environmental inputs and outputs are saved since combined heat power installation produces electricity with a higher efficiency than the public grid.
b. Another possibility is to consider the paper and excess electricity as co-products. Paper and electricity are then both “products” from the process. In an LCA this would require allocation of inputs and outputs to both products.
The reported weighted averages of the fuel consumption and emission to air associated with the paper production are calculated according to method b, as this has become common practice at the mills. This means that the fuel consumption and emissions to air do not include the production of the sold electricity and the amount of the sold electricity is not reported. This was calculated as follows: the fuel consumption and emissions to air associated with the total heat production and the net electricity used on site were allocated to the paper production.
Figure 12: CHP, Combined heat and power generation
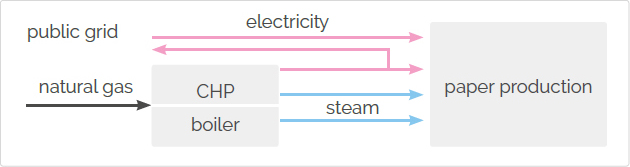
Diesel or gasoil/LPG used for internal transports are reported. Most of the energy consumed by the mills producing Kraftliner are by-products from the process and thus originates from the trees i.e. have biomass origin.
Allocation of energy to paper grades when a mill produces more than one paper grade
The energy is measured, because it is paid for. Allocation for fuels and electricity input is calculated according to energy (heat and electricity) required for the production of the different paper grades. Allocation of the other fuels, such as diesel oil used for internal transportation, was calculated according to mass production of each paper grade.